7075-T6 vs 6061-T6 Aluminum Billet 80% Lowers
When looking at 7075 vs 6061, it’s important to first understand what those numbers represent. Both contain elements such as magnesium, silicon, copper, iron, zine, the 6065 contains less zinc. The smaller content of zinc lets the 6065 weld better, however it does not have the same high strength resistance as the 7075. We will get more into why this isn't exactly important later. T6 refers to the grade of tempering (or process of hardening aluminum). Ranging from t1 to t10, the T6 grade is strengthened by heat treatment and then artificially aged. The T6 process greatly strengthens the aluminum, as well as adding rigidity, and resilience. All of these characteristics will not only aid in longevity of the life of the aluminum parts, but the rigidity will aid in increased accuracy for the shooter.
7075-T6 Aluminum
7075-T6 is a high grade aluminum commonly used in aerospace, marine, and transportation applications. Very light and extremely strong, this aluminum is pricey; but the cost is worth it when you need a high performance aluminum. However, for our applications in firearms, this grade of aluminum is a bit overkill and actually not ideal for an 80% lower. Because the 7075 is so hard, it wears out drill bits and endmills much quicker than the 6061, and just isn’t a value rich option for our customers. 7075 is also more susceptible to rust, and even though your lower will be anodized or cerakoted, those finishes can crack and scratch leaving behind bare metal.
Advantages
- High strength
- Mil Spec
Disadvantages
- Corrosion Resistance
- Price/Cost
- Workability
- Harder on tools and Endmills
6061-T6 Aluminum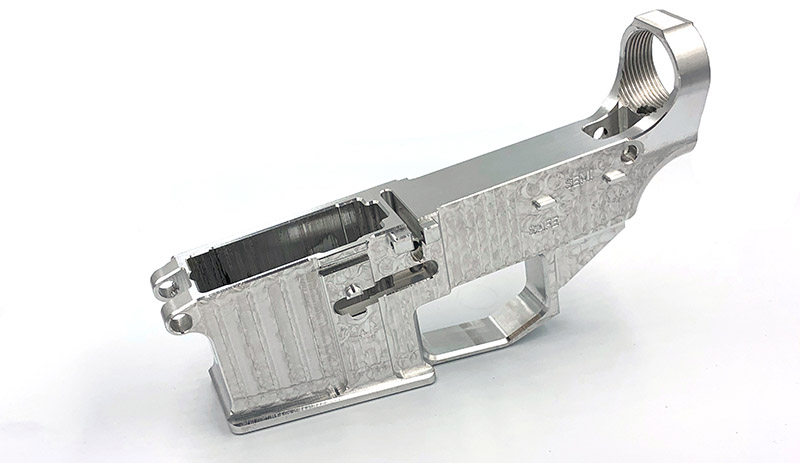
6061 is by definition a lower grade aluminum, but its lower grade in the same way that a Lamborghini is a lower grade compared to a Ferrari. For our uses in an 80% lower receiver, the 6061 aluminum is actually a better choice. It resists corrosion better than the 7075, it is more price effective for the customer, and it isn’t as hard to fabricate. Being a ‘softer” aluminum lets the customer get more life out of their end mills when finishing their 80% lower, so their hard earned money goes further. The 6061 has passed every stress test we’ve thrown at it, and no failures have ever been attributed to the grade of aluminum used.
Advantages
- Better corrosion resistance
- Offers better end mill life
- More Cost effective than 7075
- Still very strong
Disadvantages
- Technically softer than 7075
Which Material is Better for a Lower Receiver?
Here’s an analogy that helps put this comparison in perspective: The handle on most toothbrushes is made of plastic. Plastic toothbrush handles don't break under normal circumstances. You could certainly make a toothbrush out of stainless steel because it is a lot stronger than plastic, but what is the point? Stainless steel is a lot more expensive than plastic. The tooth brush isn't going to break either way, so it seems like paying extra for a stainless steel toothbrush is not worth it for most people.
So why did we choose 6061 for our 80% lowers? Well, we haven't been able to make one fail (no matter how much abuse it's been put through), they resist corrosion better, and your end mills will even last longer. And when you can build more guns for less cost, that's more money you can spend on ammo, the range, or your next build.
With an 80% Arms receiver, you can always be sure you've got the best.